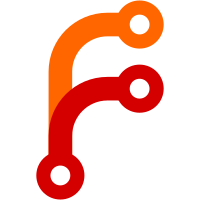
Added support for M581 and M582 commands M25 pause command can now be used inside a macro file to pause a file being printed from SD card Firmware update messages are now sent to USB and PanelDue (but the existing PanelDue firmware doesn't display them) Added gcode queue underrun counter, displayed in M122 Move diagnostic info M122 responses are now sent only to the comms channel that requested them Added support for additional firmware modules to be updated for Duet NG Corrected a possible problem with multiple incompatible gcodes being executed concurrently Support H parameter on M0 and M1 commands When executing M0/M1 commands and no print is paused, execute stop.g/sleep.g if they exist Treat M25 within the file being printed the same as M226 Added additional simulation modes to help identify bottlenecks Don't disable all interrupts when starting a new move, to reduce interrupt latency so that we can still receive data from PanelDue Moved some utility maths functions to CoreNG
56 lines
3 KiB
Text
56 lines
3 KiB
Text
; Configuration file for dc42 Kossel
|
|
|
|
; Communication and general
|
|
M111 S0 ; Debug off
|
|
M550 PKossel ; Machine name (can be anything you like)
|
|
M551 Preprap ; Machine password (used for FTP)
|
|
M540 P0xBE:0xEF:0xDE:0xAD:0xFE:0x42 ; MAC Address
|
|
;*** Adjust the IP address and gateway in the following 2 lines to suit your network
|
|
M552 P0.0.0.0 ; IP address (0 = use DHCP)
|
|
M554 P192.168.0.254 ; Gateway
|
|
M553 P255.255.255.0 ; Netmask
|
|
M555 P2 ; Set output to look like Marlin
|
|
M575 P1 B57600 S1 ; Set auxiliary serial port baud rate and require checksum (for PanelDue)
|
|
|
|
; Axis and motor configuration
|
|
M569 P0 S1 ; Drive 0 goes forwards
|
|
M569 P1 S1 ; Drive 1 goes forwards
|
|
M569 P2 S1 ; Drive 2 goes forwards
|
|
M569 P3 S0 ; Drive 3 goes backwards
|
|
M569 P4 S0 ; Drive 4 goes backwards
|
|
M574 X2 Y2 Z2 P1 ; set endstop configuration (all endstops at high end, active high)
|
|
|
|
M665 L349.5 R171.64 H493.18 B150 X0 Y0 ; set delta radius, diagonal rod length, printable radius, homed height and XY tower corrections
|
|
M666 X0 Y0 Z0 ; put your endstop adjustments here, or use auto calibration to find them
|
|
M92 X160 Y160 Z160 ; Set axis steps/mm (20 tooth pulleys, 0.9deg/step motors)
|
|
M906 X1000 Y1000 Z1000 E800 ; Set motor currents (mA)
|
|
M201 X3000 Y3000 Z3000 E1000 ; Accelerations (mm/s^2)
|
|
M203 X18000 Y18000 Z18000 E3600 ; Maximum speeds (mm/min)
|
|
M566 X600 Y600 Z600 E600 ; Maximum instant speed changes
|
|
G21 ; Work in millimetres
|
|
G90 ; Send absolute coordinates...
|
|
M83 ; ...but relative extruder moves
|
|
|
|
; Thermistors and heaters
|
|
M305 P0 T100000 B3950 R4700 H0 L0 ; Typical Chinese bed thermistor. Put your own H and/or L values here to set the bed thermistor ADC correction.
|
|
M305 P1 T100000 B4388 R4700 H0 L0 ; E3Dv6 hot end. Put your own H and/or L values here if necessary to set the first nozzle thermistor ADC correction.
|
|
M301 H0 P20 I0.5 D1000 T0.85 W150 B5 ; PID settings for the bed
|
|
M301 H1 P10 I0.10 D100 T0.50 ; PID settings for extruder 0
|
|
M570 S200 ; Allow extra heating time
|
|
|
|
; Tool definitions
|
|
M563 P0 D0 H1 ; Define tool 0
|
|
G10 P0 S0 R0 ; Set tool 0 operating and standby temperatures
|
|
M92 E420 ; Set extruder steps per mm for first and second extruders
|
|
|
|
; Z probe and compensation definition
|
|
M558 P1 X0 Y0 Z0 H3 F300 T12000 ; Z probe is IR and is not used for homing any axes, Z probe dive height 3mm, probing speed 300mm/min, travel speed 12000mm/min
|
|
G31 X0 Y0 Z1.66 P500 ; Set the zprobe offset and threshold (put your own values here). For a delta, use zero X and Y offset.
|
|
|
|
;*** If you are using axis compensation, put the figures in the following command
|
|
M556 S78 X0 Y0 Z0 ; Axis compensation here
|
|
|
|
M207 S7.0 F3600 Z0.1 ; Set firmware retraction details
|
|
M572 D0 S0.1 ; set pressure advance
|
|
|
|
T0 ; select first print head
|