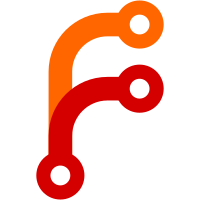
Z axis min and max limits are now enforced if the axes have been homed M665 command now shows the re-calculated delta radius and tower offsets after auto-calibration Initial and final RMS errors are now shown after delta auto-calibration Pause/resume now mostly works when absolute extruder coordinates are used Doubled the maximum length of the SD card file listing that can be sent to PanelDue Implemented zpl's Network and PrintMonitor changes including M404 (thanks, zpl) Increased default maximum instantaneous speed changes Bug fix:: if M226 was used to pause the print, the resume coordinates were not set up correctly Bug fix: when changing the travel direction, the head was sometimes slowed down more than necessary Bug fix: warm-up time was not shown correctly in DuetWebControl Bug fix: extruder drive positions were always shown as 0.0 in DuetWebControl Bug fix: incorrect PID parameters were shown in response to M301 Replaced old web interface files on SD card by DuetWebControl Modified all resume.g files to set the speed when moving to the paused head coordinates
44 lines
No EOL
3.1 KiB
Text
44 lines
No EOL
3.1 KiB
Text
; Ormerod 2 config file for dc42 Duet firmware
|
|
M111 S0 ; Debug off
|
|
M550 PMy Ormerod ; Machine name (can be anything you like)
|
|
M551 Preprap ; Machine password (currently not used)
|
|
M540 P0xBE:0xEF:0xDE:0xAD:0xFE:0xED ; MAC Address
|
|
;*** Adjust the IP address and gateway in the following 2 lines to suit your network
|
|
M552 P0.0.0.0 ; IP address (0 = use DHCP)
|
|
M554 P192.168.1.1 ; Gateway
|
|
M553 P255.255.255.0 ; Netmask
|
|
M555 P2 ; Set output to look like Marlin
|
|
G21 ; Work in millimetres
|
|
G90 ; Send absolute coordinates...
|
|
M83 ; ...but relative extruder moves
|
|
M574 X0 Y1 Z0 S1 ; set endstop configuration (Y endstop only, at low end, active high)
|
|
M906 X800 Y1000 Z800 E800 ; Set motor currents (mA)
|
|
M563 P0 D0 H1 ; Define tool 0
|
|
G10 P0 S0 R0 ; Set tool 0 operating and standby temperatures
|
|
M92 E420 ; Set extruder steps per mm (single nozzle)
|
|
;*** If you have a dual-nozzle build, remove or comment out the previous line, and un-comment the following 3 lines
|
|
;M563 P1 D1 H2 ; Define tool 1
|
|
;G10 P1 S0 R0 ; Set tool 1 operating and standby temperatures
|
|
;M92 E420:420 ; Set extruder steps/mm (dual nozzle)
|
|
;*** If you have a modulated IR probe with on-board microcontroller, change P2 to P1 in the following
|
|
M558 P2 ; Use a simple modulated Z probe (change to P1 for an intelligent Z probe)
|
|
G31 Z1.20 P500 ; Set the probe height and threshold (put your own values here)
|
|
;*** If you have a Duet board with 4.7K thermistor series resistors, change R1000 to R4700 to the following M305 commands
|
|
M305 P0 R1000 H0 L0 ; Put your own H and/or L values here to set the bed thermistor ADC correction
|
|
M305 P1 R1000 H0 L0 ; Put your own H and/or L values here to set the first nozzle thermistor ADC correction
|
|
M305 P2 R1000 H0 L0 ; Put your own H and/or L values here to set the second nozzle thermistor ADC correction
|
|
;*** Adjust the XY coordinates in the following M557 commands to suit your build and the position of the IR sensor
|
|
M557 P0 X60 Y0 ; Four...
|
|
M557 P1 X60 Y165 ; ...probe points...
|
|
M557 P2 X222 Y165 ; ...for bed...
|
|
M557 P3 X222 Y0 ; ...levelling
|
|
;M557 P4 X141 Y82.5 ; 5th probe point for levelling (un-comment this if you are using a dc42 differential IR probe)
|
|
;*** if you are using axis compensation, put the figures in the following command
|
|
M556 S78 X0 Y0 Z0 ; Axis compensation here
|
|
M201 X800 Y800 Z15 E1000 ; Accelerations (mm/s^2)
|
|
M203 X15000 Y15000 Z100 E3600 ; Maximum speeds (mm/min)
|
|
M566 X600 Y600 Z30 E20 ; Minimum speeds mm/minute
|
|
M208 X214 Y210 Z200 ; set axis maxima (adjust to suit your machine)
|
|
M208 X-8 Y0 Z-1 S1 ; set axis minimum (adjust to make X=0 the edge of the bed)
|
|
;
|
|
T0 ; select first hot end |