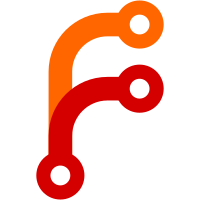
Added a sys-dc42Kossel folder in the SD card image Removed non-minimised versions of web interface files
55 lines
3 KiB
Text
55 lines
3 KiB
Text
; Configuration file for dc42 Kossel
|
|
|
|
; Communication and general
|
|
M111 S0 ; Debug off
|
|
M550 PKossel ; Machine name (can be anything you like)
|
|
M551 Preprap ; Machine password (used for FTP)
|
|
M540 P0xBE:0xEF:0xDE:0xAD:0xFE:0x42 ; MAC Address
|
|
;*** Adjust the IP address and gateway in the following 2 lines to suit your network
|
|
M552 P0.0.0.0 ; IP address (0 = use DHCP)
|
|
M554 P192.168.0.254 ; Gateway
|
|
M553 P255.255.255.0 ; Netmask
|
|
M555 P2 ; Set output to look like Marlin
|
|
M575 P1 B57600 S1 ; Set auxiliary serial port baud rate and require checksum (for PanelDue)
|
|
|
|
; Axis and motor configuration
|
|
M569 P0 S1 ; Drive 0 goes forwards
|
|
M569 P1 S1 ; Drive 1 goes forwards
|
|
M569 P2 S1 ; Drive 2 goes forwards
|
|
M569 P3 S0 ; Drive 3 goes backwards
|
|
M569 P4 S0 ; Drive 4 goes backwards
|
|
M574 X2 Y2 Z2 P1 ; set endstop configuration (all endstops at high end, active high)
|
|
|
|
M665 L349.5 R171.64 H493.18 B150 X0 Y0 ; set delta radius, diagonal rod length, printable radius, homed height and XY tower corrections
|
|
M666 X0 Y0 Z0 ; put your endstop adjustments here, or use auto calibration to find them
|
|
M92 X160 Y160 Z160 ; Set axis steps/mm (20 tooth pulleys, 0.9deg/step motors)
|
|
M906 X1000 Y1000 Z1000 E800 ; Set motor currents (mA)
|
|
M201 X3000 Y3000 Z3000 E1000 ; Accelerations (mm/s^2)
|
|
M203 X18000 Y18000 Z18000 E3600 ; Maximum speeds (mm/min)
|
|
M566 X600 Y600 Z600 E600 ; Maximum instant speed changes
|
|
G21 ; Work in millimetres
|
|
G90 ; Send absolute coordinates...
|
|
M83 ; ...but relative extruder moves
|
|
|
|
; Thermistors and heaters
|
|
M305 P0 T100000 B3950 R4700 H0 L0 ; Typical Chinese bed thermistor. Put your own H and/or L values here to set the bed thermistor ADC correction.
|
|
M305 P1 T100000 B4388 R4700 H0 L0 ; E3Dv6 hot end. Put your own H and/or L values here if necessary to set the first nozzle thermistor ADC correction.
|
|
M301 H1 P10 I0.10 D100 T0.50 ; PID settings for extruder 0
|
|
M570 S200 ; Allow extra heating time
|
|
|
|
; Tool definitions
|
|
M563 P0 D0 H1 ; Define tool 0
|
|
G10 P0 S0 R0 ; Set tool 0 operating and standby temperatures
|
|
M92 E420 ; Set extruder steps per mm for first and second extruders
|
|
|
|
; Z probe and compensation definition
|
|
M558 P1 X0 Y0 Z0 H3 F300 T12000 ; Z probe is IR and is not used for homing any axes, Z probe dive height 3mm, probing speed 300mm/min, travel speed 12000mm/min
|
|
G31 X0 Y0 Z1.66 P500 ; Set the zprobe offset and threshold (put your own values here). For a delta, use zero X and Y offset.
|
|
|
|
;*** If you are using axis compensation, put the figures in the following command
|
|
M556 S78 X0 Y0 Z0 ; Axis compensation here
|
|
|
|
M207 S7.0 F3600 Z0.1 ; Set firmware retraction details
|
|
M572 D0 S0.1 ; set pressure advance
|
|
|
|
T0 ; select first print head
|